13 Years Manufacturer Rubber shoe cover-M for Czech Factories
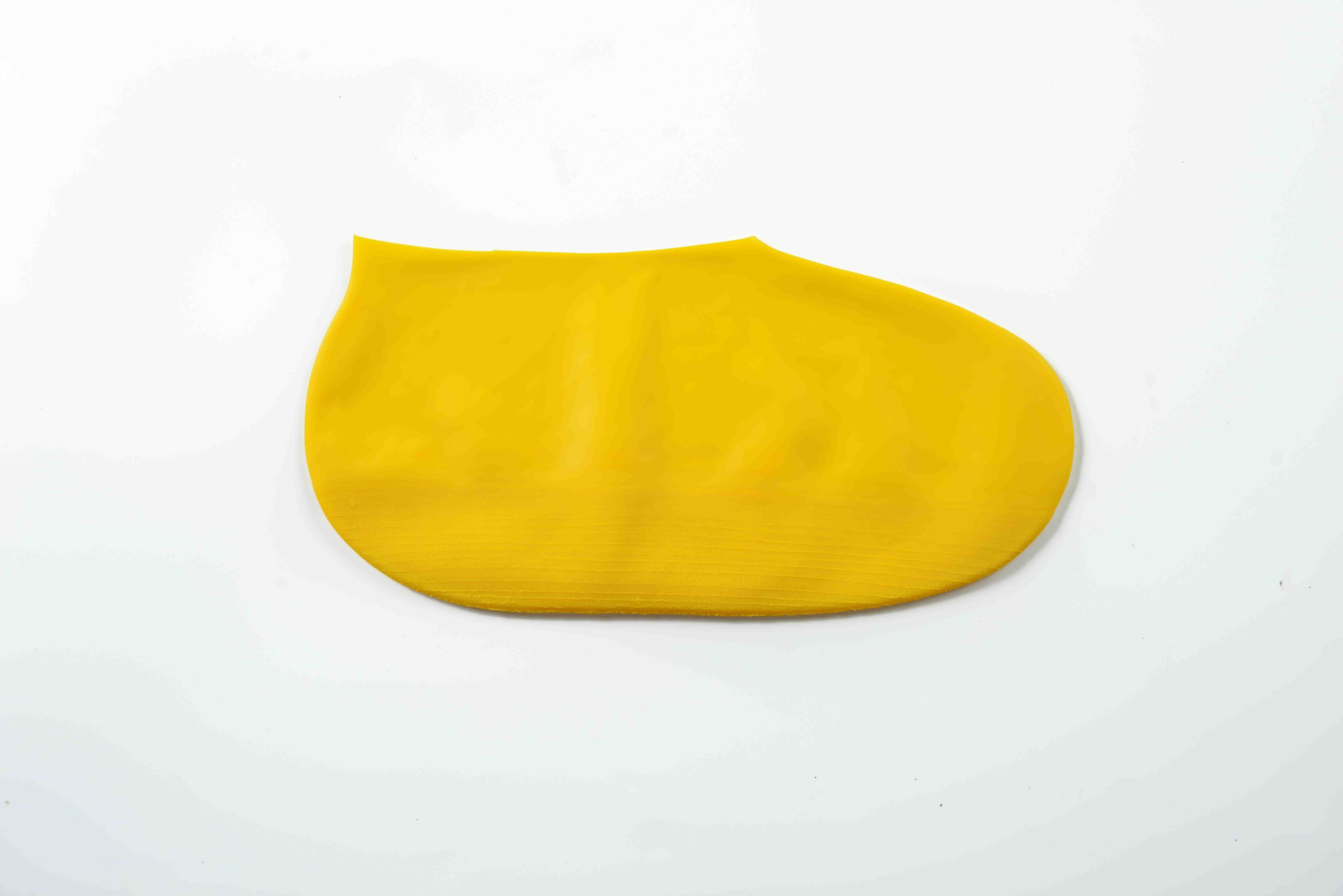
Short Description:
Rubber shoe cover, made of 100% natural rubber, wrinkling sole for slip resistance, water proof, good elasticity, good resistance against acid and alkali, non-toxic, No stimulating smell. They can be widely used in industry, agriculture, food processing, etc. 4 sizes. Different colors are available. Package: 100 pairs/case.
Product Detail
FAQ
Product Tags
Our development depends on the advanced equipment, excellent talents and continuously strengthened technology forces. 13 Years Manufacturer Rubber shoe cover-M for Czech Factories, With a wide range, good quality, reasonable prices and good service, we will be your best business partner. We welcome new and old customers from all walks of life to contact us for future business relationships and achieving mutual success!
Rubber shoe cover, made of 100% natural rubber, wrinkling sole for slip resistance,
water proof, good elasticity, good resistance against acid and alkali, non-toxic, No stimulating smell.
They can be widely used in industry, agriculture, food processing, etc.
4 sizes. Different colors are available. Package: 100 pairs/case.
FAQ Content
http://www.fashion-style.com.pl/prod.php?lang=pl&fs=1186
http://www.fashion-style.com.pl/prod.php?lang=en&fs=1186
Roberto is in this video. After a short presentation of the company, he explains how trilaminate drysuits are produced.
Enjoy it and please comment below.
“My name is Roberto Scerbo
I’m the owner and founder of Rofos.
I founded this Company 32 years ago.
We started with gloves socks and wetsuits to me and to colleagues and friends who were doing competitive spearfishing.
These 25 years of competitiveness obviously gave to me a depth knowledge of neoprene using it personally.
The passion pushed us over the years to expand the range and the quality of products, widening of course also the headquarters becoming a benchmark in the diving industry.
In 2010 we decided to face a new challenge developing our first trilaminate drysuit dedicated to technical diving.
The manufacturing of templates begins with the selection of the fabrics and cutting the jigs in various sizes.
The real production begins with the cutting of the fabric and reinforcements.
In the early years we used to cut by hand.
Nowdays we introduced an electric cutter to maximize the precision.
At this time we proceed with the application of the dry zipper and the neck seal, until the fabric is still lying on the table to ensure an optimal application.
The third stage involves the application of the pockets and reinforcements by sewing and the assembly of the various pieces.
Then we proceed with the application of wrists and boots The heat welding is the key step to ensure the watertight integrity of the drysuit, so, obviously, we dedicate close attention this step.
Every single suit is then tested in a tank to control the effective sealing of each single seam.
The spirit of the Company is to continue to grow creating more and more performing and reliable products.”